In this article:
- M Series Zone 2 Panel PC for Hazardous Area Applications
- What is Explosion-Proof Product Design Technology?
- Factory Certified by UL and CSA Quality Management System
- NEC and IEC Certifications NEC (National Electric Code)
- IEC (International Electrochemical Commission)
- Enhancing Safety and Efficiency in the Petroleum Industry: Hazardous HMIs and Rugged Computers
- Safety and Standards
- Winmate Possesses Advanced Expertise In Manufacturing and Developing Explosion-proof Data Processors.
- What Are ATEX Grade Rugged Computers?
- ATEX Certified Rugged Computers for Hazardous Environments
- Possible Applications
- Winmate Explosion-proof Solutions Now Include The M-Series (12.1” / 15” / 17” / 19”/ 21.5” /23.8” ) Family ATEX/C1D2 Modular Design Panel PCs.
- Main Features
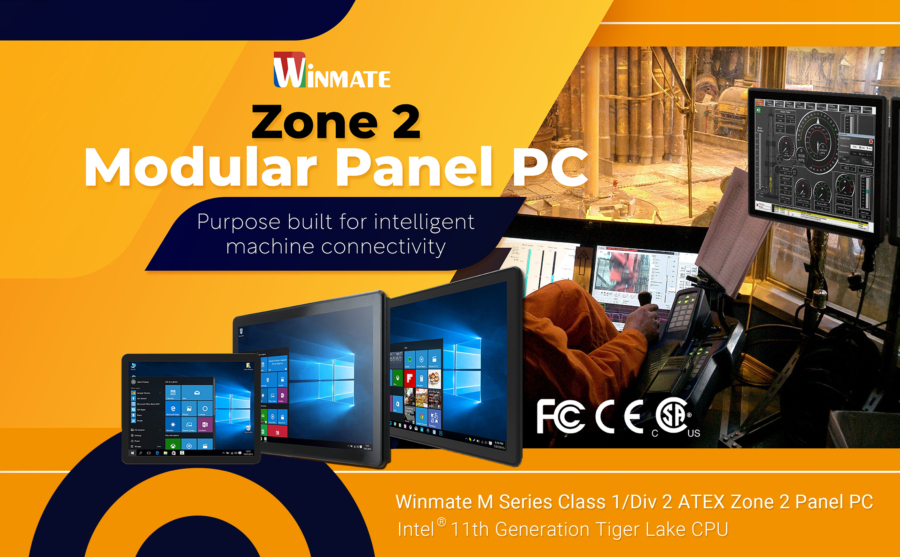
M Series Zone 2 Panel PC for Hazardous Area Applications
Winmate, a global leader in industrial computing solutions, introduce its latest innovation, the M Series Zone 2 Panel PC. Engineered to meet the stringent requirements of hazardous area applications, this state-of-the-art Panel PC delivers exceptional performance and durability.
Industry Challenges
The oil & gas industry represents one of the most hazardous and demanding work environments, necessitating utmost caution and precision. With risks posed to both personnel and equipment, ensuring dependable and accurate monitoring becomes paramount to maintaining a safe operational atmosphere.
Winmate provides a range of Explosion-Proof panel computers specially designed for remote data collection, process visualization, and control, catering to the unique needs of this industry. These secure technologies are geared towards bolstering the productivity, safety, and efficiency of oil refineries. With effective process control measures in place, operation costs can be reduced, ultimately leading to increased profitability.
What is Explosion-Proof Product Design Technology?
In countries across the globe, laws and regulations mandate that electrical equipment must adhere to strict safety standards when operating in potentially flammable or explosive environments. These hazardous areas are characterised by the presence of flammable gases or vapours, flammable liquids, combustible dust, or ignitable fibres or flying particles. The oil and gas production operations and facilities are prime examples of such hazardous locations, where risks of fire and explosion are prevalent. It is crucial for all electrical equipment used in these settings to possess fire and explosion protection capabilities, along with necessary safety certifications.
Factory Certified by UL and CSA Quality Management System
Winmate factory is UL and CSA certified with the Quality Management System.
To meet the safety qualification, Winmate offers ATEX and Class 1 Division 2 (C1D2) certified solutions for maintaining safe operations and collecting detailed, sensitive data in remote rig and pipeline locations.
For the classification of the equipment, Winmate generally uses both the North American National Electric Code (NEC) and the European ATEX directive.
NEC and IEC Certifications NEC (National Electric Code)
According to OSHA, NEC defines hazardous locations as those areas where fire or explosion hazards may exist due to flammable gases or vapours, flammable liquids, the combustible dust of ignitable fibres or filings.
NEC classified hazardous locations in three ways; type, condition, and nature.
IEC (International Electrochemical Commission)
IEC defines the flammable gases and vapours and then flammable dust, each of this type are assigned into three different zones and each zone then requires equipment built for category I, II or III.
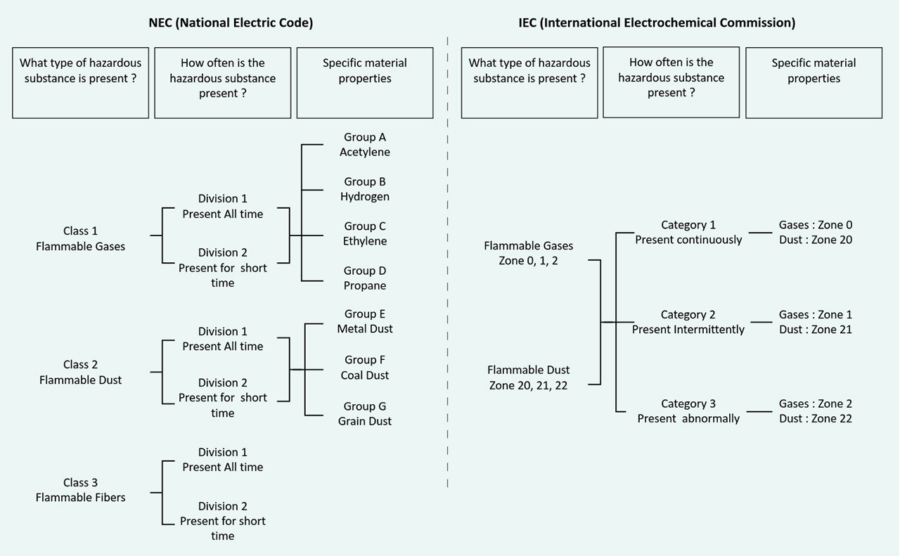
Intrinsic Safety Schematic Design
In the pursuit of utmost safety and compliance, the electronic system’s schematic design must guarantee that, under any fault conditions, the temperature will never reach levels that could potentially ignite explosive gases. At our company, our team of expert engineers specialises in designing intrinsic safety schematics specifically tailored for our explosion-proof product line.
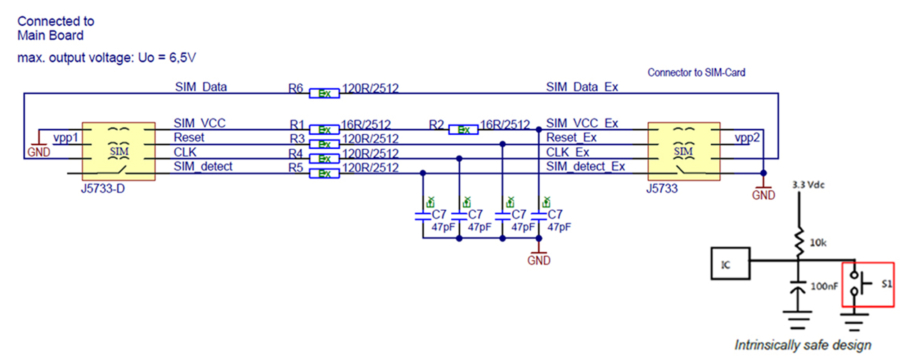
Non-Sparking Device
Intrinsically safe design serves as a crucial safeguard against the ignition of hazardous atmospheres, such as explosive gas or dust. This comprehensive safety approach entails allowing only low voltages and currents to enter the hazardous area, while simultaneously ensuring no significant energy storage is possible.
No-Air Potting Process
Potting is a vital procedure that involves filling an entire electronic assembly with a solid or gelatinous compound, offering resistance against shock, vibration, and protection from moisture and corrosive agents. By employing this advanced technique, Winmate ensure that your electronic substrate remains resilient even in challenging environments, free from potential damage caused by vibrations or other adverse conditions.
ATEX Safety and Standards
Oil rigs and remote pipeline locations rank among the most perilous and demanding work environments worldwide. When seeking electronic devices to support operations in such settings, it becomes imperative that these devices fulfill three essential requirements:
- Provide advanced system monitoring even in the most challenging conditions.
- Accurately identify and track assets and communicate data from remote sites.
- Withstand the highest scrutiny of certification and inspection Because the conditions are risky for personnel and equipment, reliable and accurate monitoring is crucial to maintaining safe operations.
In addition, computers at these working locations must also keep detailed data on, for example, petroleum exploration and transportation. To meet the safety qualification, Winmate offers ATEX and Class 1 Division 2 (CID2) certified solutions for maintaining safe operations and collecting detailed, sensitive data in the remote rig and pipeline locations.
In the petroleum exploration and production industry, upstream processes demand sophisticated and streamlined Human-Machine Interfaces (HMIs) tailored to handle hazardous conditions. These HMIs serve crucial functions such as measurement-while-drilling (MWD), logging operations, downhole functions, torque control, and directional drilling. However, advancements in hazardous processing technology now empower designers and operators with access to vital performance data and equipment management, even in rough operating conditions.
To ensure seamless operations, companies increasingly turn to sleek and lightweight hazardous computers and displays. These devices can be easily installed for additional control, conveniently positioned closer to the sizeable machinery and drilling sites. By embracing these modern HMIs, petroleum exploration and production operations achieve enhanced efficiency, safety, and reliability, propelling the industry forward.
Enhancing Safety and Efficiency in the Petroleum Industry: Hazardous HMIs and Rugged Computers
The petroleum industry encompasses a wide range of services, including distribution, storage, blending, inventory management, and additive injection, to cater to the needs of end-users. In a manner similar to hazardous technology used in upstream processes, operations in the midstream sector rely on the same robust computers. These rugged devices effectively monitor performance and control processing technology for various operations, including those in challenging environments such as tanker ships, pipelines, and storage facilities.
A notable example of the value of fully rugged computers is their application in monitoring and managing fuel flow within the midstream sector. These reliable technologies provide easy access to flow metrics and pipeline performance data, enabling operators to swiftly detect and respond to critical issues, such as leaks, ensuring efficiency and safety.
In the petroleum refining sector, the safety of specific locations is established by hazardous place classification bodies. North America employs the NFPA distinction body, while Europe adheres to the IECEX ATEX Directive. These bodies define the settings and ensure safe installation and operational practices, minimizing the risk of electrical hazards.
In the oil and gas industry, selecting the most appropriate categories for hazardous HMIs is of paramount importance. For routine operations where combustible concentrations of gas or vapours may be present, the hazardous computer must be tested and certified for IECEX Zone 1 environments or Class I, Division 1 environments.
Both in the midstream and complex sectors, hazardous computers play a crucial role in maintaining operations without compromising safety. These robust devices are essential in preventing breakdowns and potential explosions, ensuring seamless and efficient operations throughout the industry. Trust in our reliable hazardous HMIs to uphold safety standards and enhance productivity in your oil and gas operations.
The oil and fuel market demands modern technology and exclusive electrical wiring and power parts that reduce electric breakdowns or even blasts to protect people and equipment. This industry-specific crafted style for the source establishment allows unsafe PPCs to work efficiently and correctly in regions where combustible fuels, dirt, or even water vapours might exist. For the oil and gas industry, the most relevant classifications for hazardous HMIs are as follows:
For regular working operations where there are ignitable concentrations of flammable gasses or vapours are typically.
Quality Management System
Winmate factory is UL and CSA certified with Quality Management System.
UL and CSA certified
Product Testing & Certifications
To meet the safety qualification, Winmate offers ATEX and Class 1 Division 2 (CID2) certified solutions for maintaining safe operations and collecting detailed, sensitive data in the remote rig and pipeline locations.
For the equipment classification, Winmate generally uses both the North American National Electric Code (NEC) and the European ATEX directive.
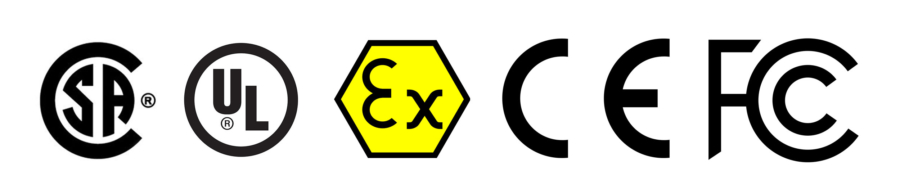
Safety and Standards
NEC (National Electric Code) |
According to OSHA, NEC defines hazardous locations as those areas where fire or explosion hazards may exist due to flammable gases or vapors, flammable liquids, combustible dust, or ignitable fibers or flyings. NEC classified hazardous locations in three ways; type, condition, and nature. |
IEC (International Electrochemical Commission) |
IEC defines the flammable gases and vapors, and then flammable dust, each of this type are assigned into three different zones, and each zone then requires equipment built for category I, II or III. |
Winmate Possesses Advanced Expertise In Manufacturing and Developing Explosion-proof Data Processors.
Extreme operating environment
Rugged computers excel in delivering advanced system monitoring capabilities, even under the most demanding conditions. Designed to thrive in challenging environments, these devices are equipped to withstand potential explosive atmospheres, extreme temperature variations, and exposure to water and rain. Trust in the durability and performance of rugged computers for optimal performance in tough operating conditions.
Remote locations
Rugged laptop and tablet PCs play a vital role in accurately identifying and tracking assets while facilitating real-time data monitoring and communication from remote sites. These robust devices ensure seamless data transfer, enabling efficient asset management and timely communication, even in challenging environments.
Environmental regulations
All the workstations for oil & gas applications must pass the highest scrutiny of certification and inspection.
What Are ATEX Grade Rugged Computers?
Oil rigs and remote pipeline locations pose significant challenges, being among the most hazardous work environments globally. Winmate’s rugged computers are purposefully designed to excel in such demanding settings, whether on an oil refiner or a drilling rig. These computers come equipped with ATEX Zone 2 and Class 1 Division 2 (C1D2) certifications, ensuring utmost safety and compliance.
Winmate offers ATEX Zone 2 and Class 1 Division 2 (C1D2) certified panel computers, embedded processors, and industrial displays tailored for remote data collection, process visualisation, and control. With these safe and reliable technologies, oil refineries can enhance productivity, safety, and overall efficiency. By effectively controlling processes, companies can reduce operational costs and maximise profits.
Our computing solutions have been successfully deployed in refining and petrochemical applications, supporting numerous companies in improving their productivity, safety, and efficiency.
ATEX Certified Rugged Computers for Hazardous Environments
ATEX certified rugged computers are engineered to endure the most extreme conditions found in hazardous environments, including oil refineries, chemical plants, and mining operations. These robust devices are specifically designed to operate reliably in harsh settings, offering exceptional resistance against dust, water, shocks, and other contaminants.
Here are some of the key benefits of using ATEX certified rugged computers in hazardous environments.
In hazardous environments, the importance of reliability cannot be overstated, as downtime can prove costly and dangerous. ATEX certified rugged computers are equipped with top-notch components, enabling them to withstand shocks and vibrations with ease, ensuring their steadfast operation in the most demanding conditions. Trust in the unmatched performance of ATEX certified rugged computers to maintain seamless and secure operations, even in the harshest environments.
In hazardous environments, ATEX certified rugged computers play a pivotal role in enhancing productivity. These advanced devices facilitate remote data collection, process visualization, and control, allowing operators to monitor and manage critical processes from a safe distance. By enabling such seamless operations, the risk of accidents and downtime is significantly reduced, while overall efficiency is improved.
Moreover, ATEX certified rugged computers are meticulously designed to meet stringent regulatory requirements for hazardous environments. These devices adhere to ATEX standards, guaranteeing full compliance with regulations for usage in hazardous areas. By incorporating ATEX certified rugged computers into your operations, you can rest assured that your practices align with regulatory requirements, mitigating the risk of potential fines or penalties. Prioritize safety and compliance with our ATEX certified rugged computers for a secure and efficient working environment in hazardous settings.
ATEX certified rugged computers offer versatility for application in a wide range of hazardous environments. These durable devices can be seamlessly utilized in various industries, such as oil refineries, chemical plants, mining operations, pharmaceutical plants, power generation facilities, offshore platforms, drilling rigs, gas processing plants, and hazardous waste facilities.
These are just a few examples, but the versatility and safety features of ATEX certified Panel Pcs and other rugged computers prove indispensable for individuals working in hazardous environments. These advanced devices provide an unparalleled level of safety, durability, reliability, and productivity, all while guaranteeing compliance with regulatory requirements. With their specialized components and certifications, ATEX certified rugged computers stand as the optimal choice for anyone seeking secure operations in explosive atmospheres.
By law and legislation across countries worldwide, electrical equipment must adhere to stringent safety standards for operation in potentially flammable or explosive environments. These hazardous areas may consist of flammable gases or vapours, flammable liquids, combustible dust, or ignitable fibres. Oil and gas production operations and facilities frequently encounter these hazards and dangers.
Given that flammable or explosive substances can be present in varying quantities at any time, ensuring fire and explosion protection becomes crucial. For this reason, safety certifications are mandatory for all electrical equipment used in these operations. Complying with these vital regulations guarantees the utmost safety in hazardous work environments, reducing the risk of potential accidents and ensuring secure operations in the oil and gas industry.
For a more in-depth explanation of Class 1/Div 2 ATEX Zone 2 Certifications
Possible Applications
ATEX and Class 1 Division 2 certified Touch Screen Panel PCs are designed to be used in potentially hazardous environments where explosive gases, vapours, or dust may be present. Due to their rugged and intrinsically safe nature, they find applications in various industries to ensure safety and reliable operation. Some possible applications include:
- Oil and Gas Industry: ATEX and Class 1 Division 2 certified Panel PCs can be used in drilling rigs, refineries, and petrochemical plants to monitor processes and control equipment in potentially explosive atmospheres.
- Chemical Processing: These Panel PCs can be used in chemical plants where volatile substances are handled to facilitate process monitoring and control.
- Mining: In underground mines or locations with combustible dust, the Panel PCs can be used for data visualization, equipment monitoring, and automation.
- Pharmaceutical Manufacturing: In pharmaceutical facilities that handle flammable materials, these certified Panel PCs can ensure accurate process control and regulatory compliance.
- Paint and Coatings Industry: In areas where flammable solvents are used, the Panel PCs can be utilized for quality control, recipe management, and production monitoring.
- Food and Beverage Processing: ATEX and Class 1 Division 2 certified Panel PCs can be applied in food processing plants to control equipment and monitor production processes.
- Waste Treatment Facilities: These Panel PCs can be used to monitor and control equipment in waste treatment plants, where hazardous gases may be present.
- Aerospace Industry: In environments like aircraft hangars where flammable materials may be present, the Panel PCs can be utilized for maintenance and monitoring tasks.
- Transportation and Logistics: In potentially hazardous storage or transportation environments, these Panel PCs can be used for tracking and monitoring purposes.
- Offshore and Marine: ATEX and Class 1 Division 2 certified Panel PCs can be installed on offshore platforms, ships, and vessels where there is a risk of explosive atmospheres.
These are just a few examples, but the versatility and safety features of ATEX certified Panel Pcs and other rugged computers prove indispensable for individuals working in hazardous environments. These advanced devices provide an unparalleled level of safety, durability, reliability, and productivity, all while guaranteeing compliance with regulatory requirements. With their specialized components and certifications, ATEX certified rugged computers stand as the optimal choice for anyone seeking secure operations in explosive atmospheres.
By law and legislation across countries worldwide, electrical equipment must adhere to stringent safety standards for operation in potentially flammable or explosive environments. These hazardous areas may consist of flammable gases or vapours, flammable liquids, combustible dust, or ignitable fibres. Oil and gas production operations and facilities frequently encounter these hazards and dangers.
Given that flammable or explosive substances can be present in varying quantities at any time, ensuring fire and explosion protection becomes crucial. For this reason, safety certifications are mandatory for all electrical equipment used in these operations. Complying with these vital regulations guarantees the utmost safety in hazardous work environments, reducing the risk of potential accidents and ensuring secure operations in the oil and gas industry.
For a more in-depth explanation of Class 1/Div 2 ATEX Zone 2 Certifications
Winmate Explosion-proof Solutions Now Include The M-Series (12.1” / 15” / 17” / 19”/ 21.5” /23.8” ) Family ATEX/C1D2 Modular Design Panel PCs.
Expand Panel PC Capabilities With Modular Design
The Winmate M Series Zone 2 Panel PC boasts an Intel 11th Generation Tiger Lake CPU, ensuring exceptional and efficient computing power to meet the demands of challenging industrial environments. This high-performance processor enables seamless multitasking and swift data processing, empowering operators to work with speed and precision.
The M Series Panel PC also stands out with its signature true flat display screen, featuring an edge-to-edge design that seamlessly blends aesthetics with functionality. Moreover, the aluminium housing of the panel undergoes anti-corrosion treatment, guaranteeing long-lasting durability even in the harshest operating conditions.
Superior Sealing With Front IP65 Protection Against Dust and Water
The Winmate M Series Zone 2 Panel PC is engineered to conquer the challenges of hazardous environments, providing superior sealing with front IP65 protection against dust and water. This robust protection guarantees reliable operation and minimizes the risk of damage caused by environmental factors. Beyond its resilience and functionality, the Winmate M Series Zone 2 Panel PC offers flexible connectivity options.
Supporting a wide range of 9-29 V DC input, it adapts to various power supply scenarios with ease. The quick and easily removable 2.5″ SSD Bay Slot ensures efficient storage management and data transfer. Additionally, the Panel PC supports PCIe x4 Card, expanding its capabilities to meet specific application requirements. Certified for Hazardous Locations
The Winmate M Series Zone 2 Panel PC holds Class 1, Division 2, and IECEx certifications, guaranteeing adherence to safety standards for hazardous area applications. With these certifications, operators can work in potentially explosive environments with peace of mind, knowing that the Panel PC meets stringent safety regulations. Trust in the Winmate M Series Zone 2 Panel PC for secure and reliable operations in hazardous settings.
The M Series is available in several sizes: 12.1”, 15”, 17”, 19″, 21.5”and 23.8”.
Main Features
- Intel 11th Generation Tiger Lake UP3 Core CPU HMI Panel PC
- Signature true flat display screen with edge-to-edge design
- Aluminum, anti-corrosion treated housing
- Superior sealing with front IP65 protection against dust and water
- Projected Capacitive Multi-Touch Screen (PCAP)
- Fanless Design, C1D2 HMI Panel PC
- Support wide range 9-29 V DC input
- Quick & Easy Removable 2.5” SSD Bay Slot
- Support PCIe x4 Card
- C1D2 & IECEx certificated, Compliance with ATEX grade zone 2