In this article:
- Introduction
- MIL-STD-461 Overview: Ensuring Electromagnetic Compatibility
- MIL-STD-810 Overview: Environmental Engineering Considerations
- MIL-DTL-38999/1 Overview: High-Performance Circular Connectors
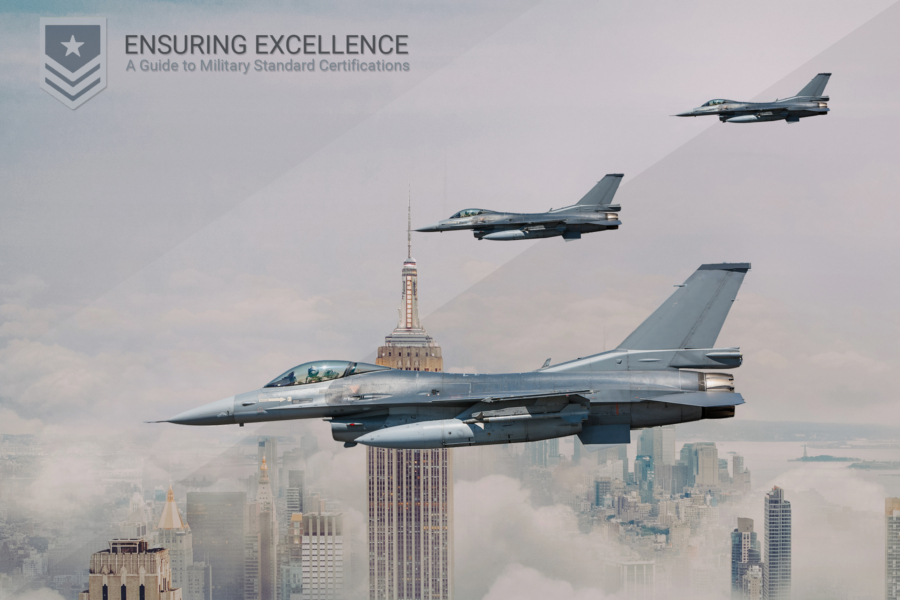
Introduction
Defence computing solutions need to be truly rugged and be MIL-STD 810F/G and MIL-STD 461E/F compliant. They need to be able to withstand extreme environmental conditions such as high and low temperature, shock, vibration, and humidity and meet the requirements for controlling electromagnetic interference. The protection from electromagnetic interference is further enhanced by the application of ITO EMI shielding.
With such systems, power connectors that are such as MIL-DTL-38999/1 military-grade, can be used to ensure reliable power and rugged mechanical performance. Assured Systems understands the needs of the defense industry and provides solutions to industrial challenges:
- Extreme environmental conditions:For MIL-STD-810G compliance, products are tested against extreme environmental conditions such as high and low temperature, shock, vibration, humidity.
- Electromagnetic interference:For MIL-STD-461F compliance, detailed testing specification ensures that the product meets the control of electromagnetic interference.
- Unstable power supply: Broad power input and isolation to protect Panel PC and rugged tablets from power surges.
Detection of illicit signals and electromagnetic interference assumes paramount importance in military operations, given that virtually every electronic device, from a common cellphone to a critical navigation component in a stealth jet, emits electromagnetic fields that could potentially jeopardise safety, operational efficiency, or secure communications.
To address this pressing concern, the DoD established the Electromagnetic Compatibility Program, with the overarching objective of integrating electromagnetic compatibility considerations into the research and development efforts of the defense industry.
Over time, all three branches of the military have joined forces to develop updated and expanded iterations of the standard. This collaborative effort culminated in the latest version, MIL-STD-461G.
MIL-STD-461 is a United States Defence Standard that describes how to test equipment for electromagnetic compatibility.
Specifically, MIL-STD-461F details testing specifications to ensure the conducted emissions (CE), conducted susceptibility (CS), radiated emissions (RE), and radiated susceptibility (RS) of a system can meet the requirements for the control of electromagnetic interference.
- MIL-STD-461 Method – CE101/CE102: Conducted Emissions
- MIL-STD-461 Method – RE101/RE102: Radiated Emissions
- MIL-STD-461 Method – CS101/CS106/CS109/CS114/CS115/CS116: Conducted Susceptibility
- MIL-STD-461 Method – RS101/RS103: Radiated Susceptibility
MIL-STD 461 Testing
The “H” in MIL-STD-810H for instance, indicates that it is the eighth revision of the standard. Each revision of MIL-STD-810 incorporates updates and improvements based on advancements in technology and lessons learned from field experience.
MIL-STD-810H covers a broad range of environmental conditions, including temperature, humidity, altitude, vibration, shock, acceleration, rain, sand and dust exposure, solar radiation, fungus, and more. The standard provides detailed testing procedures and performance criteria for each environmental condition, allowing manufacturers to assess and demonstrate the durability and reliability of their equipment.
MIL-STD-461 Overview: Ensuring Electromagnetic Compatibility
Military Standard 461 (MIL-STD-461) is a set of standards developed by the U.S. Department of Defense (DoD) to establish requirements for electromagnetic compatibility (EMC) and electromagnetic interference (EMI) control for military systems and equipment.
The goal, as aforementioned, is to ensure that electronic systems can operate effectively in their intended operational environments without being adversely affected by electromagnetic interference or causing interference to other systems.
Structure of MIL-STD-461
MIL-STD-461 is structured into multiple documents, each addressing specific aspects of EMC/EMI testing and control. Some key components include:
- MIL-STD-461G: Is the most recent version, outlining the general requirements for EMC/EMI control.
- Test Methods: Specific test methods are detailed in MIL-STD-461, such as the use of antennas, conducted susceptibility tests, radiated emissions tests, and more.
Tests Carried Out in MIL-STD-461
- Conducted Susceptibility Tests
- CS101 – Conducted Susceptibility, Power Leads: This test evaluates the susceptibility of a device to conducted low-frequency signals on its power leads.
- CS114 – Conducted Susceptibility, Bulk Cable Injection: Bulk cable injection tests assess the susceptibility of a device to disturbances injected directly into its cables.
- CS116 – Conducted Susceptibility, Damped Sinusoidal Transients: This test examines a system’s vulnerability to damped sinusoidal transients on its power leads.
- Radiated Susceptibility Tests
- RS101 – Radiated Susceptibility, Magnetic Field: This test assesses a system’s susceptibility to magnetic fields in its operational environment.
- RS103 – Radiated Susceptibility, Electric Field: Electric field susceptibility tests evaluate a system’s response to electric field disturbances.
- RS105 – Radiated Susceptibility, Transient Electromagnetic Field: This test assesses a system’s resilience against transient electromagnetic fields.
- Radiated Emissions Tests
- RE101 – Radiated Emissions, Magnetic Field: This test measures the magnetic field emissions from a system.
- RE102 – Radiated Emissions, Electric Field: Electric field emissions are assessed to ensure compliance with EMC requirements.
- RE103 – Radiated Emissions, Antenna Spurious and Harmonics: This test examines unwanted emissions from the system’s antennas.
- Conducted Emissions Tests
- CE101 – Conducted Emissions, Power Leads: This test measures conducted emissions on power leads.
- CE102 – Conducted Emissions, Power Leads, 10 kHz to 10 MHz: It assesses conducted emissions in a broader frequency range.
Suitable Applications
MIL-STD-461 is crucial for a wide range of military applications where electronic systems are employed. Some notable applications include:
- Aerospace Systems: Aircraft and spacecraft often utilize complex electronic systems. MIL-STD-461 ensures that these systems can operate reliably in the presence of electromagnetic interference.
- Ground Vehicles: Military ground vehicles, such as tanks and personnel carriers, rely on various electronic components. Compliance with MIL-STD-461 ensures that these components can function without being compromised by electromagnetic interference.
- Naval Systems: Ships and submarines have a multitude of electronic systems on board. MIL-STD-461 testing is essential to guarantee the robustness of these systems in maritime environments.
- Communication Systems: Military communication systems, including radios and other transmitters, must adhere to MIL-STD-461 to ensure that they can operate efficiently without causing interference to other electronic devices.
- Weapon Systems: Electronic components in weapon systems, including guidance systems and control electronics, undergo MIL-STD-461 testing to ensure their reliability and performance in diverse operational environments.
MIL-STD-461 plays a pivotal role in the development and testing of military electronic systems, ensuring that they can operate effectively in complex and challenging electromagnetic environments.
The comprehensive set of tests outlined in the standard addresses various aspects of electromagnetic compatibility and interference, providing a robust framework for the design and evaluation of military hardware. Adherence to MIL-STD-461 is not only a requirement for military contracts but also a critical factor in ensuring the success and reliability of military systems in the field.
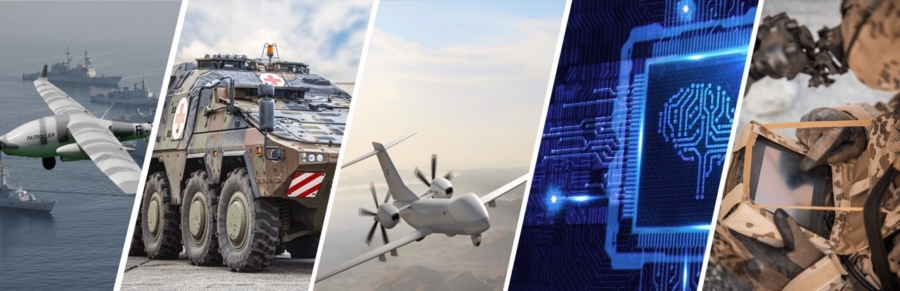
MIL-STD-810 Overview: Environmental Engineering Considerations
Military Standard 810 (MIL-STD-810) is a series of standards developed by the U.S. Department of Defense (DoD) that establishes testing methods and procedures for the environmental engineering of military equipment. The standard addresses a wide range of environmental conditions, providing guidelines for testing and evaluating the performance of military systems and equipment under various challenging scenarios.
Structure of MIL-STD-810
MIL-STD-810 is organised into two main parts:
- Part One: This section outlines the environmental laboratory test methods used for military equipment.
- Part Two: This section provides tailoring instructions to guide the selection of test methods based on the specific environmental conditions the equipment is expected to encounter.
Environmental Factors Covered
MIL-STD-810 addresses a comprehensive set of environmental factors, including:
- Temperature
- High Temperature (Method 501): Evaluates the performance of equipment in high-temperature conditions.
- Low Temperature (Method 502): Tests the equipment’s functionality in low-temperature environments.
- Humidity
- High Temperature, Low Humidity (Method 507): Assesses equipment performance in high-temperature, low-humidity conditions.
- Low Temperature, Low Humidity (Method 514): Tests the equipment’s response in low-temperature, low-humidity environments.
- Vibration
- Vibration (Method 514): Examines the impact of mechanical vibrations on equipment.
- Shock
- Shock (Method 516): Evaluates the equipment’s ability to withstand mechanical shocks.
- Rain
- Rain (Method 506): Tests the equipment’s resistance to rain and other liquid exposure.
- Sand and Dust
- Blowing Sand and Dust (Method 510): Assesses the equipment’s durability in sandy and dusty environments.
- Altitude
- High-Altitude (Method 511): Evaluates performance at high altitudes.
- Fungus
- Fungus (Method 508): Tests the equipment’s susceptibility to fungal growth.
- Salt Fog
- Salt Fog (Method 509): Assesses resistance to salt fog, common in maritime environments.
- Explosive Atmosphere
- Explosive Atmosphere (Method 511): Examines equipment performance in potentially explosive atmospheres.
Suitable Applications
MIL-STD-810 is applicable to a wide range of military and non-military applications where equipment is subjected to challenging environmental conditions. Some notable applications include:
- Aerospace Systems: Aircraft and spacecraft undergo MIL-STD-810 testing to ensure they can withstand temperature extremes, vibrations, and other environmental factors during flight.
- Ground Vehicles: Military vehicles, including tanks and trucks, are tested to ensure they can operate in diverse terrains and withstand shocks and vibrations.
- Naval Systems: Ships and submarines are subjected to MIL-STD-810 testing to ensure they can endure harsh maritime conditions, including salt fog and high humidity.
- Communication Systems: Military communication equipment, such as radios and antennas, undergoes testing to ensure reliability in various environmental scenarios.
- Electronic Devices: Military-grade laptops, computers, and other electronic devices are tested to withstand temperature variations, humidity, and other environmental challenges.
MIL-STD-810 is a critical standard in the development and testing of military equipment, providing a systematic approach to assess the impact of environmental conditions on performance. The comprehensive testing methods outlined in the standard enable designers and engineers to create robust and resilient systems that can operate effectively in diverse and challenging environments. Adherence to MIL-STD-810 is essential for ensuring the reliability and durability of military equipment, ultimately contributing to the success of military operations across air, land, and sea.
MIL-DTL-38999/1 Overview: High-Performance Circular Connectors
Military Specification 38999/1 (MIL-DTL-38999/1) is a standard set by the U.S. Department of Defense (DoD) that defines the requirements for high-performance circular connectors. These connectors are widely used in military and aerospace applications where durability, reliability, and resistance to harsh environmental conditions are crucial.
Structure of MIL-DTL-38999/1
MIL-DTL-38999/1 is part of a larger series of specifications, collectively known as the MIL-DTL-38999 series. The /1 designation specifically pertains to the wall mount receptacles. The standard encompasses various classes, materials, and performance levels to accommodate diverse application requirements.
Key Features and Requirements
- Durability and Construction
- Materials (Section 3): Specifies the materials used for various connector components, ensuring they meet stringent military standards for durability and corrosion resistance.
- Shell Design (Section 4): Outlines the design and construction of the connector shell, providing details on its durability and resistance to environmental factors.
- Electrical Performance
- Contact Arrangements (Section 4): Defines the arrangement and configuration of contacts within the connector, ensuring proper electrical performance.
- Electrical Characteristics (Section 5): Specifies the electrical properties of the connectors, such as voltage, current, and insulation resistance.
- Environmental Resistance
- Temperature (Section 3): Defines the temperature range within which the connector must operate, ensuring functionality in extreme temperature conditions.
- Environmental Sealing (Section 4): Outlines the requirements for environmental sealing, preventing the entry of moisture, dust, and other contaminants.
- Mechanical Performance
- Insert Retention (Section 4): Specifies the force required to remove or insert contacts, ensuring a secure connection.
- Mating and Unmating Forces (Section 4): Defines the forces required for mating and unmating connectors, considering the need for reliability and ease of use.
Suitable Applications
MIL-DTL-38999/1 connectors find applications in a variety of military and aerospace systems where robust and reliable connections are critical. Some notable applications include:
- Aerospace and Aviation: These connectors are commonly used in aircraft and spacecraft systems, providing reliable connections for avionics, communication, and power distribution.
- Military Ground Vehicles: MIL-DTL-38999/1 connectors are employed in military vehicles, including tanks and armored personnel carriers, ensuring durable and secure connections in harsh terrain.
- Shipboard Systems: In maritime environments, where exposure to saltwater and harsh weather conditions is prevalent, these connectors are utilized for shipboard systems, navigation, and communication.
- Ground Support Equipment: In military operations, ground support equipment requires rugged connectors for reliable power and data connections in field conditions.
- Missile Systems: MIL-DTL-38999/1 connectors are integrated into missile systems, providing a robust interface for critical electronics and control systems.
MIL-DTL-38999/1 plays a crucial role in ensuring the reliability and performance of circular connectors in demanding military and aerospace applications. The specification’s focus on durability, electrical performance, and environmental resistance makes it a trusted standard for designers and manufacturers seeking connectors that can withstand the rigors of harsh operational environments. Adherence to MIL-DTL-38999/1 is essential for achieving consistent and robust connections in military and aerospace systems, contributing to the overall success and reliability of these critical applications.
The MIL-DTL-38999 series includes various parts that cover different aspects and types of connectors. As of my last knowledge update in January 2022, the following are some of the key parts within the MIL-DTL-38999 series:
- MIL-DTL-38999/1: Wall mount receptacles (as previously discussed).
- MIL-DTL-38999/2: Cable connectors (plugs) with crimp contacts.
- MIL-DTL-38999/3: Jam nut receptacles with crimp contacts.
- MIL-DTL-38999/4: Straight plug connectors with crimp contacts.
- MIL-DTL-38999/5: Straight plug connectors with printed circuit contacts.
- MIL-DTL-38999/6: Wall mount receptacles with printed circuit contacts.
- MIL-DTL-38999/7: Jam nut receptacles with printed circuit contacts.
- MIL-DTL-38999/8: Straight plug connectors with socket contacts.
- MIL-DTL-38999/9: Wall mount receptacles with socket contacts.
- MIL-DTL-38999/10: Jam nut receptacles with socket contacts.
- MIL-DTL-38999/11: Straight plug connectors with crimp rear-release contacts.
- MIL-DTL-38999/12: Wall mount receptacles with crimp rear-release contacts.
- MIL-DTL-38999/13: Jam nut receptacles with crimp rear-release contacts.
- MIL-DTL-38999/14: Straight plug connectors with PC tail rear-release contacts.
- MIL-DTL-38999/15: Wall mount receptacles with PC tail rear-release contacts.
- MIL-DTL-38999/16: Jam nut receptacles with PC tail rear-release contacts.
Each of these parts specifies different configurations and features of connectors, including contact types, attachment methods, and environmental sealing requirements. Designers and engineers select the appropriate part based on the specific needs of their applications, taking into consideration factors such as electrical requirements, environmental conditions, and mechanical considerations.
It’s important to note that standards and specifications can be updated or revised, so it’s advisable to check with the latest version of these series of ‘MIL’ Standards or other official documentation for the most current information.